Ethically made in Australia
Both our labels are ethically Made in Australia by Collier Clothing in Brunswick, Melbourne.
We choose certified organic and natural fibres and make in small batch runs, which means no over production and much reduced fashion waste.
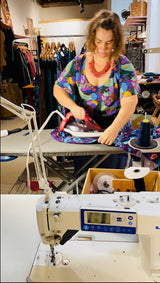
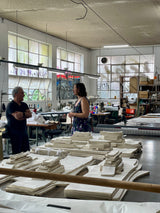
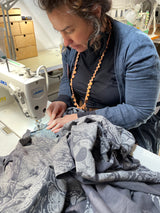
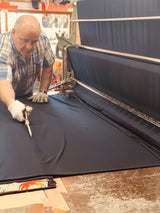
Sustainability Story
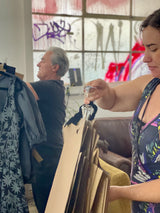
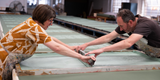
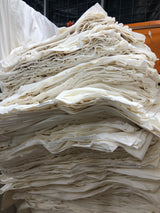
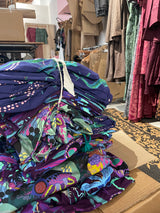
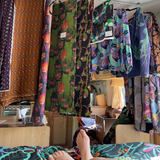
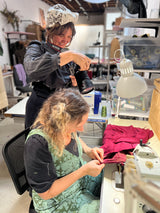
Made in Melbourne
I've been working with Collier Clothing for 4 years now. Sam and Jim have been in the biz for over 30 years and know exactly what they're doing.
There are many boxes to tick when finding the right working relationship, such as, workable production numbers, fair wages, quality of work, timely delivery, pleasant communication and the list goes on... I am very happy that I have found a good match with Collier.
Hand Screen Printing
We chose screen printing for the Dalee Ella collection to recreate the texture of Dalee's lino prints.
We have been super lucky to partner with Printink Studio in Collingwood, Melbourne where Nadia and Jason literally print each meter of our fabric by hand.
The hand feel of the ink sitting on top of our certified organic cotton knit, cannot be replicated in any other way and we love that you can literally feel the artwork.
We exclusively use Permaset inks which are water based, non-toxic and free of harmful chemicals.
Base Fabric
Our plain stretch cotton knit is not only certified organic cotton, but it is knitted in Melbourne and dyed with certified organic dyes.
There are only a handful of Australian mills left in the country, so this is a special thing.
I have been using ABMT's stretch knit for over 15 years. It's high quality, feels great, moves with your body and has amazing longevity.
Storyline digital prints
While screen printing is beautiful, it has limitations with how many colours you can use in one print. Thats why I found Senboo textiles, a small digital fabric printer and ethical fashion manufacturer in China.
I was very mindful when choosing a new fabric supplier that they specialise in GOTS certified organic cotton, use eco-friendly inks, and have OKEO Tex certification.
It took me about three years to find the right printer and I have been wear testing their fabrics for that long and am very happy with the feel, print quality and longevity.
Natural Fibres
I only use organic and natural fibres as polyester is literally plastic. It's 2025, you can't be using plastic in clothing anymore, plus natural fibres feel way better to wear.
It's an ongoing process, finding fabrics which perform in the best possible way with the best environmental credentials.
Its not perfect, but I do make the best decisions I possibly can and am constantly researching how to improve fabric choices.
If there is one thing I have learnt, its that you cannot rush into using all new fabrics without testing, and this is a lengthy process. Slow and steady is the way forward.
In house sample making
I have been honing my sewing and design skills for over 20 years.
Understanding just how much goes into perfecting fit and construction gives me an insight into the value of clothing which other designers who don't sew may not have.
I believe that is integral to helping change the narrative around clothing from being disposable, to something we care for.
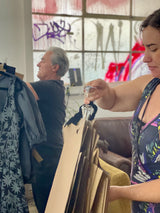
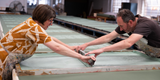
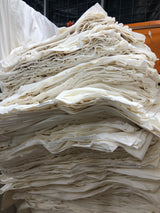
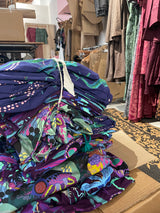
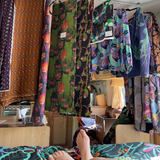
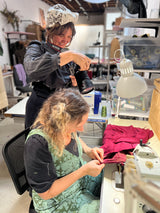
Made in Melbourne
I've been working with Collier Clothing for 4 years now. Sam and Jim have been in the biz for over 30 years and know exactly what they're doing.
There are many boxes to tick when finding the right working relationship, such as, workable production numbers, fair wages, quality of work, timely delivery, pleasant communication and the list goes on... I am very happy that I have found a good match with Collier.
Hand Screen Printing
We chose screen printing for the Dalee Ella collection to recreate the texture of Dalee's lino prints.
We have been super lucky to partner with Printink Studio in Collingwood, Melbourne where Nadia and Jason literally print each meter of our fabric by hand.
The hand feel of the ink sitting on top of our certified organic cotton knit, cannot be replicated in any other way and we love that you can literally feel the artwork.
We exclusively use Permaset inks which are water based, non-toxic and free of harmful chemicals.
Base Fabric
Our plain stretch cotton knit is not only certified organic cotton, but it is knitted in Melbourne and dyed with certified organic dyes.
There are only a handful of Australian mills left in the country, so this is a special thing.
I have been using ABMT's stretch knit for over 15 years. It's high quality, feels great, moves with your body and has amazing longevity.
Storyline digital prints
While screen printing is beautiful, it has limitations with how many colours you can use in one print. Thats why I found Senboo textiles, a small digital fabric printer and ethical fashion manufacturer in China.
I was very mindful when choosing a new fabric supplier that they specialise in GOTS certified organic cotton, use eco-friendly inks, and have OKEO Tex certification.
It took me about three years to find the right printer and I have been wear testing their fabrics for that long and am very happy with the feel, print quality and longevity.
Natural Fibres
I only use organic and natural fibres as polyester is literally plastic. It's 2025, you can't be using plastic in clothing anymore, plus natural fibres feel way better to wear.
It's an ongoing process, finding fabrics which perform in the best possible way with the best environmental credentials.
Its not perfect, but I do make the best decisions I possibly can and am constantly researching how to improve fabric choices.
If there is one thing I have learnt, its that you cannot rush into using all new fabrics without testing, and this is a lengthy process. Slow and steady is the way forward.
In house sample making
I have been honing my sewing and design skills for over 20 years.
Understanding just how much goes into perfecting fit and construction gives me an insight into the value of clothing which other designers who don't sew may not have.
I believe that is integral to helping change the narrative around clothing from being disposable, to something we care for.
Blog posts
Wanderer Pants: My Personal Fave (and Why You’ll Love Them Too)
What I’ve Learned After 2 Months of Business Mentoring
Good design is a sustainability practice
Why We Manufacture Ethically (And What That Means)
Why Our Black Sidewalk Pants Will Never Go Out of Style
Why Natural Fibres Cost More—And Why They're Worth It
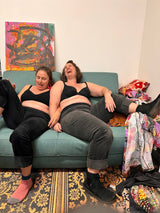
Wanderer Pants: My Personal Fave (and Why You’ll Love Them Too)

What I’ve Learned After 2 Months of Business Mentoring

Good design is a sustainability practice

Why We Manufacture Ethically (And What That Means)

Why Our Black Sidewalk Pants Will Never Go Out of Style
